
I had seen a number of laser cut business cards on this sight that sandwiched gears between sheets to create motion, but as the look was the important part (applying to a visual company, not an engineering firm) and more parts meant more possible points of failure, I decided instead to use a rotating cam approach. In creating my system, I wanted an automated situation in which when I moved the wand, the arrow inside the case would rotate upward and be revealed. There are more interesting chrome, brass, neoprene and paper connectors, gaskets and washers in that section than you can shake a stick at. When searching out fasteners, don’t forget to visit the plumbing section. My piece is made of white, black and brushed aluminum acrylic, so I picked out materials and fittings that complimented those colors. Now it’s time to select the hardware you'll use to hold your case together and give it a little more awesome bling-ness.Ī trip to the hardware is in order. Everything came with a protective paper coating on it, which I really wanted to take off, but I knew I would be puttering around with this thing for a while before sending it in, so I left the paper on to avoid scratches. If you’ve never experienced the excitement of waiting for, then receiving a “kit” of something you’ve designed yourself, I have to tell you, it’s pretty awesome. There was a one week turnaround time on the parts.
COOL OTOMATA REGISTRATION
While the Mylar was too thin to prove that my item would work mechanically, it did prove that all of my registration holes and slots were going to line up, as well as my bottom window and gear/signature artwork. If you are working on a mechanical project or a project where fit or specific tolerance is a requirement – it is well worth the time and minor added expense to have them run you a Mylar test cut. After a couple of emails and minor design tweaks, we ran a test cut on Mylar (clear film pieces shown in bottom right photo) to check the alignment of everything. My contact there was Arthur Rodrigues, who was extremely helpful. In searching the web, I found Pololu Robotics and Electronics in Las Vegas, Nevada (.) They do a number of really cool things, including sell parts for the sort of projects found here on Instructables. Not owning a laser cutter :( I needed to find a company that could help with the actual cutting of the acrylic. (Gratuitous explosion at end adds no additional value, but was brought to you at no additional cost.)
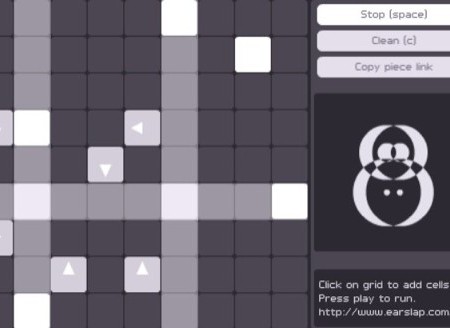

COOL OTOMATA SOFTWARE
I found when trying to explain this project to friends, they were having a hard time picturing it - A quick export of the paths that would be used for cutting into 3d rendering software gave me a feel of how things would line up and perform as well as provide a visual to folks of what I was trying to accomplish. If you're looking to add little sculptural bits, or do something not so flat, take a look at 123D make on this website. If you're going to do a basic flat stack type case, software programs like Autodesk AutoCAD, or Adobe Illustrator work beautifully. Base your pin holes diameters on standard nut and bolt sizes, as a visit to your hardware will be required to keep your case together. Use a piece of software that allows you to draw in separate LAYERS and build each successive piece off that original set of paths, assuring that the exterior edges and knockouts (locations of the pins that hold the stack together) line up.
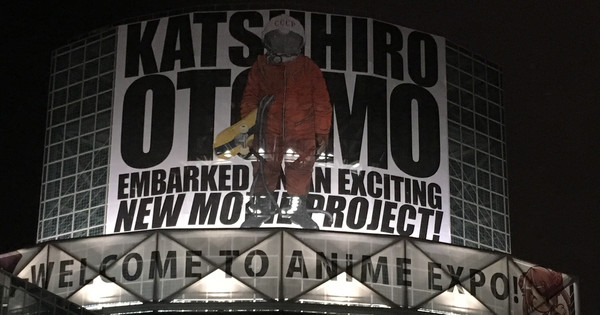
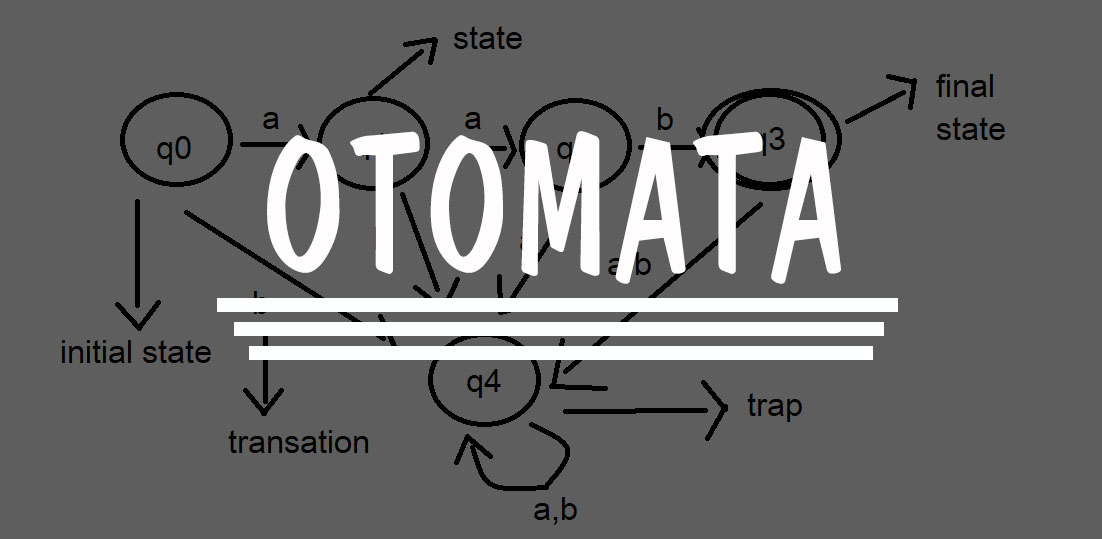
Layout one “master” piece to use as a template - in my instance, the back of the case as it defined the shape and boundaries of the piece, as well as all hardware locations.
